Reconditioning of Spare Parts
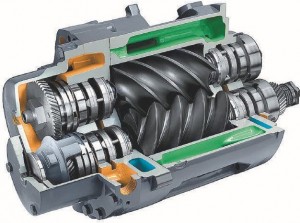
Details
Reconditioning of the compressor is essential for keeping the valves in good condition and to enhance the performance of the compressors. If the compressors are not kept under maintenance on a regular basis, it not only leads to deterioration of the valves but also raise the operating costs. Compared to entirely replacing the valves, a far better solution is to recondition them. One of the initiative which has been taken by Aeroflon is to recondition the expensive valves which forms the arteries of the compressors during hours of predicament.
![]() |
De-greasing, Washing with environment friendly solvent & blasting |
![]() |
Inspection and Clearance. |
![]() |
Reconditioning process, including machining / lapping etc keeping designed dimension intact
Replacing with new internals. |
![]() |
Assembly and Air Leak Testing |
![]() |
Packaging and labeling |
1) INSPECTION AND CLEARANCEThe initiation of the reconditioning process begins with an elaborate and intricate procedure of inspection and clearance. The valves which are subjected to refurbishing are sent to Oriental workshops to be dismantled, and cleaned for inspection. Major parts like seats and guards are thoroughly inspected for any kind of fault or erosion. The valves which are under suspicion of having faults at a minimal level are exposed to magnetic particle testing which are used in revealing hairline cracks. 2) RECONDITIONING PROCESSIt is prerogative of oriental to take utmost care of the valves for the benefit of the compressors as well as the client. One of the prime parts of the reconditioning is the removal of the traces of foreign deposits. The Valve seats and Guards are subjected to shot peening for the cleansing of the foreign sediments and deposition. If necessary the valves are then re machined as per the norms of the original manufacturers design, keeping the exact tolerance to maintain the original characteristics of the performance. To ensure precision of the flatness and the perfection of the finished result, all the valve seat sealing faces are lapped as per the standards.
3) REPLACING WITH NEW INTERNALSAll internal components like valve plates, valve springs, spacers etc are replaced with new ones. 4) LEAK TESTINGAll the components are screened through the process of leak testing. Compressed air is passed through the valves and the valves are given the green signal if only the leaks are within permissible limit. The leak test can be made in view of the representative of the client company if prior arrangements are made. 5) PACKAGING AND LABELINGThe reconditioned valves are provided with coats of chemicals which help in prevention of rust or any means of corrosion. These are packed and labeled in a way so that no harm can come to the valves during transit or storage. |
Benefits for our Clients
![]() |
The customer can achieve savings up to 60% in several cases. |
![]() |
|
![]() |
|
Best at Aeroflon
Enquire NOW!
We are sure that this decision will affect your business in a great way. So why waiting?